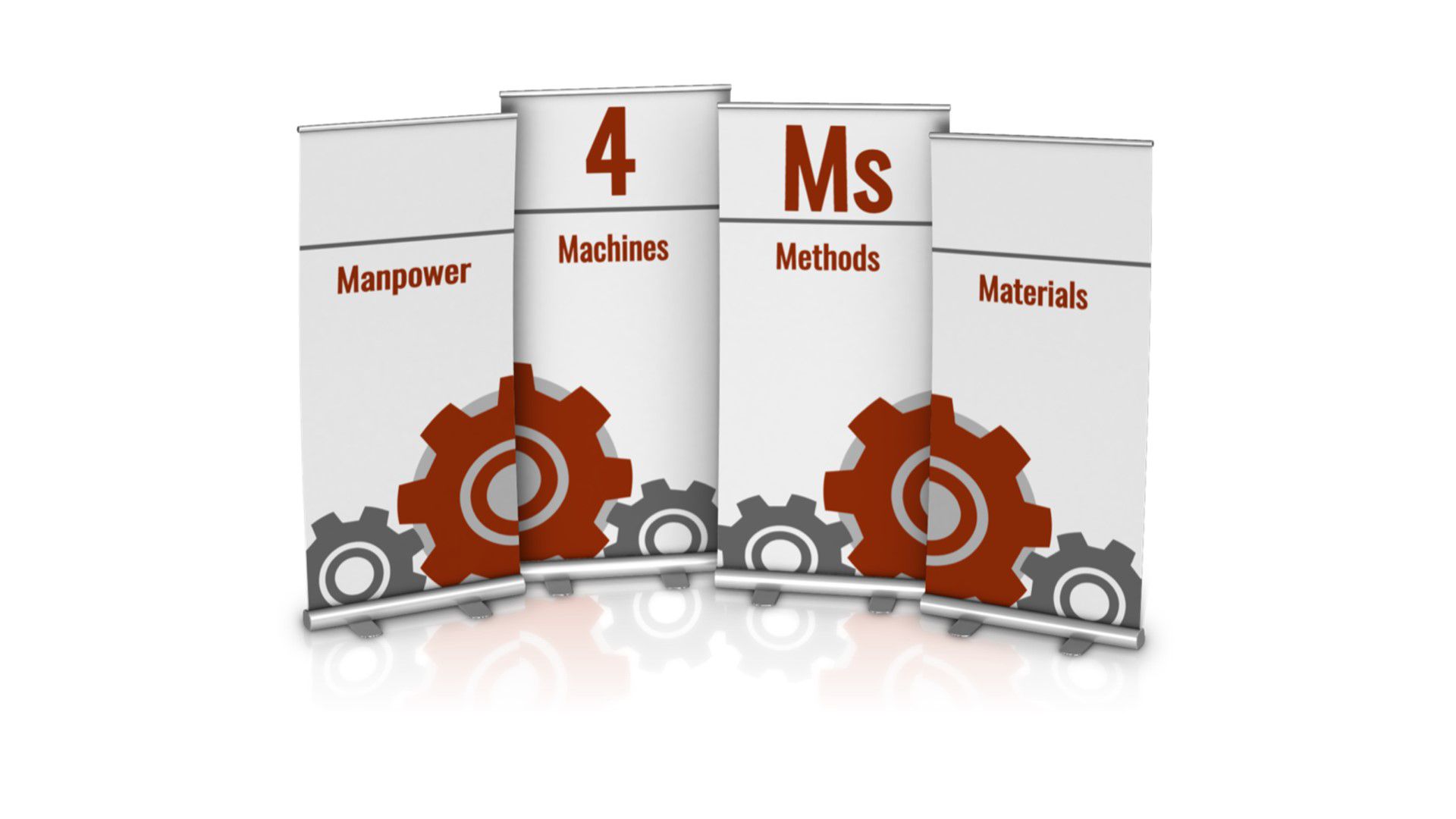
The Four M’s of a Successful COVID Startup
When starting a manufacturing process after an extended COVID-19 driven shutdown, there is nothing more important than properly controlling the four M’s of production: Machine, Material, Methods and Manpower. For many manufacturing processes it will have been eight weeks or more since the last time they produced a product. A lot can happen over that time period that affects the Machines, Materials, Methods and Manpower of a manufacturing process.
Machines – Preventative Maintenance Program Records Are The Key To Getting Ready Quickly
Machinery that is in good working order is critical for a manufacturing process is to start up with a minimal amount of problems after an extended shutdown. If you have a good Preventative Maintenance (PM) program, it can provide you with valuable information that you can use to make sure your machinery is in good working order before you start the manufacturing process. Key elements of the existing PM program to use are:
- Listing of Outstanding Required Repairs That Have Not Been Completed: A good PM program finds a lot of issues. It is not uncommon where all the issues found cannot be completed for one reason or another. Consequently, the issues often must be prioritized. It has been a long time since the process was shut down and many of the important issues that were on everybody’s mind are now forgotten. All outstanding maintenance issues must be assessed for importance and prioritized for their completion before the process is started.
- Listing of Past Due Inspections: Many inspections that should have been performed have not due to the shutdown. It is important that a review be conducted of all past due inspections and a determination made about which ones must be done before startup and which ones should be rescheduled.
If you don’t have a PM program, use this as an opportunity to start one. Lubrication and cleanliness of sections of the equipment that could affect the quality of the product should be at the top of list. Don’t be surprised if you find animals where you do not expect them. Checking of safety related equipment function is critical. Make sure that everything that must move to protect the safety of the workers still moves.
Materials – Your consumables might have changed. Find this out late and it will cause countless problems
The condition of any consumables that may have been affected by the environmental conditions they were stored in must be checked. For many companies, the COVID-19 shutdowns came with very little warning and consequently very little time to do the things that should be done when a manufacturing facility is entering into an extended shutdown. If you find improperly stored materials, they must either be tested to make sure they are still acceptable or disposed of.
If you have consumables that have a shelf life, make sure you check their expiration dates. There are two critical reasons for this. The first is you do not want to make products with expired materials. The second is you don’t want to have to shut down because you had to throw out materials because they were expired and now you do not have the inventory to run.
Methods – Implementing social distancing is going to change your process. Have you changed your methods and procedures to match?
Many companies have a considerable investment of resources into implementing lean manufacturing into their organization. The companies who have successfully implemented lean manufacturing have seen reductions in the seven forms of waste: over-production, inventory, motion, waiting, transportation, rework and over-processing. To save “transportation” waste, many workstations have been moved closer together.
The manufacturing floor may have to be significantly modified to implement the required social distancing to protect the workers. If equipment is not moved, barriers that did not exist before may have to be put up to provide worker protection. New work procedures may need to be developed because of these changes.
Manpower – Protecting your worker’s safety is critical. Make sure you do it correctly!
The biggest danger to the manufacturing operation is infection of the workforce. The COVID-19 virus is very contagious and large portions of a workforce could become infected quickly. The thermal testing that many manufacturing companies are planning to use to detect people with fevers as an indication of a COVID-19 infection will only be about 25% effective in detecting infected people.
Proper facial coverings are the key to preventing infection of the workforce. Due to the danger of the COVID-19 virus, proper facial coverings are now more important than safety glasses and ear plugs. The company must be careful and purchase a mask that protects the worker from infection and that has adequate filtration. N95 Respirators and equivalent facial coverings that protect workers from infection are in short supply. They will be in shorter supply when the COVID-19 infections start to rise again as expected due to “America opening” and the increased exposure of people to the virus. Many companies will be forced to purchase “cloth masks” or allow employees to use their own. It is important to put the proper controls in place to ensure the proper cloth masks are in use if you use cloth masks. Training on what a proper facial covering looks like for COVID-19 may be required.
Conclusion – Control the 4Ms to ensure a good startup
The key to a great startup is proper control of the 4 M’s: Machines, Materials, Methods and Manpower. When you attempt to control the 4 M’s, protecting your workers from infection will probably be the most difficult task.
For more information on how to determine if the facial covering you plan to use is appropriate, please watch
Find Out If You Have the Right Mask in Two Minutes
If you have not selected a mask yet, please watch
Five Things You Need to Know Before You Make or Buy a Mask